The unexpected secret weapon of the steel industry: Butt Welding (And why its NOT what you think!!)
When you hear the term “butt welding” your mind might conjure up some rather humorous images. But in the steel industry, it’s no laughing matter – it’s a serious business that plays a critical role in keeping the world standing tall (quite literally). So, let’s dive into the nitty gritty of butt welding, and explore why this oddly named technique is a superstar in the world of steel.
Firstly, lets clear the air – no, butt welding doesn’t involve any behind-the-scenes shenanigans. It’s a welding technique where two pieces of metal are joined together at their ends (or butts, hence the name) to create a seamless, continuous bond. Think of it as the steel industry’s version of a strong handshake, only a more permanent one.
When it comes to holding things together, butt welding is like Hercules, the joint created by this method is as strong if not stronger than the metal its connecting, it’s a bond that can withstand the pressures of time and weather without breaking a sweat.
Lets be honest – cutting costs is a priority for any industry. Butt welding steps in here, reducing material waste and eliminating the need for extra fasteners. Imagine a process where you don’t need expensive joiners to keep things together, like making a sandwich with no crusts, just the good stuff in the middle.
In industries where safety and performance are non-negotiable, precision is key. Butt welding doesn’t just connect; it fuses with laser like accuracy. The result? Joints are leak proof, tight and reliable.
Butt welding may not have the flashiest name in the steel industry, but it sure does deliver where it counts. Its strong, cost-effective, versatile and precise – the perfect combination for any steel project. Next time you see a structure or vehicle, remember, butt welding likely had a hand in making it all possible.
So here’s to butt welding – keeping the steel industry together, one strong, seamless joint at a time.
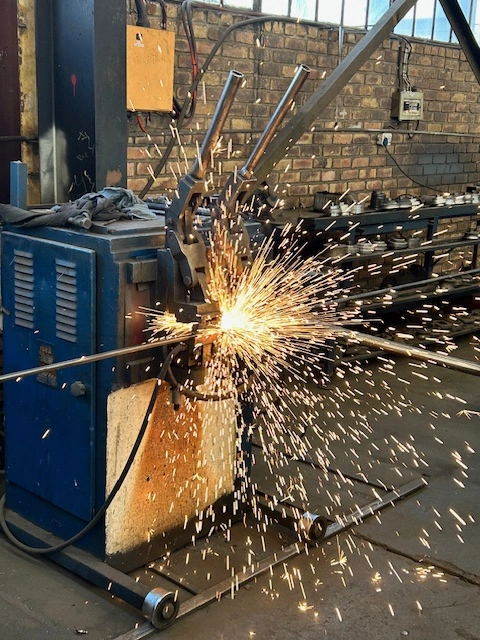
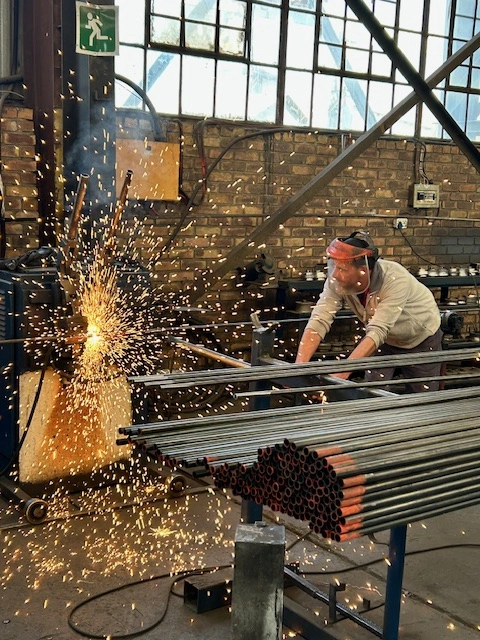